Decarbonising aluminium
What do buildings, boats, cars, planes, soda cans, mobile phones, computers, appliances and food packaging have in common? All are made with aluminium, a lightweight, recyclable and highly versatile metal that’s an unmissable part of our everyday lives.
Yet producing aluminium generates up to six times more carbon emissions than steel and requires huge amounts of electricity. Little wonder then that the industry is looking at ways to reduce its emissions in line with global targets to slow down climate change.
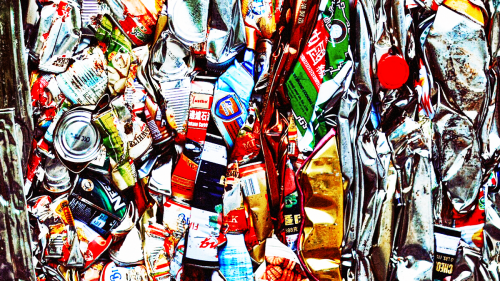
Setting the course to net zero
As one of the leading financiers of the sector, ING has joined forces with other industry players to draw up a framework that will support aluminium’s transition to net-zero emissions. The Aluminium Climate-Aligned Finance Working Group is the latest initiative by banks and the Rocky Mountain Institute (RMI) to decarbonise high emissions industrial sectors. In 2021, ING led the net-zero initiative for the steel industry.
“ING is committed to aligning our portfolio with global climate goals to keep global temperatures from rising more than 1.5 degrees and ultimately to net-zero emissions by 2050. But there’s no clear guidance yet on what this means for the aluminium sector or how to get there. That’s why we’re engaging with other industry players on this project to find a metric and future trajectory that will bring us to net zero,” says Meint Boschloo, director in ING’s Metals, Mining & Fertilisers commodities team.
The lead banks (ING, Societe Generale and Citi) are currently recruiting more financial institutions to join the working group, which will establish the measurement methodology, emissions benchmark, data, reporting framework and governance structure for the sector’s climate-aligned finance framework. Ultimately the aim is for financial institutions to adopt the framework in early 2023 and set global practices on climate for aluminium finance.
Why are we doing this?
Emissions from aluminium production can range from around 3 tons of CO2 per ton of aluminium up to around 19 tons. The huge differences lie mostly in the type of electricity used during the smelting process. Whereas some aluminium producers, notably in Europe and North America, use renewable energy sources such as hydropower, others use gas while the biggest polluters – accounting for half of the market – still use coal-fired electricity.
However industrial users of aluminium, such as car manufacturers (like BMW) and mobile phone makers (e.g. Apple) are progressively changing the market, pushing for carbon-free or low-carbon aluminium. This demand, along with proposed carbon taxation, is helping to advance the agenda for decarbonisation. It also has accelerated opportunities for banks like ING who have been engaging with their clients on the topic of sustainability for several years.
Given its many uses, there is a growing demand for this strong but lightweight metal. Electric car makers, for example, are switching to aluminium to bring down the weight of the vehicles. This means production is unlikely to slow down any time soon. It leaves lenders with a conundrum – how to greenify and support the growth of the full value chain, including those companies with a relatively large footprint (which could increase the carbon footprint of the lender’s own portfolio). Helping these companies to transition towards net-zero will have an enormous positive impact on the planet. Answers to the dilemma will have to be found in cutting-edge refining/smelting technology and renewable based energy. All with the aim of producing carbon-free aluminium, ultimately benefitting the entire sector as well as the energy transition.
Recycling aluminium
One big advantage of aluminium is that it’s infinitely recyclable. This, combined with its light weight and resistance to corrosion, make it a sustainable material to use. According to the US Aluminum Association, almost 75% of all the aluminium ever produced is still in use today. And recycling aluminium uses just 5% of the energy it takes to produce it from the ground.
How is aluminium produced?
Aluminium starts out as bauxite ore, a red clay-like soil found in a belt around the equator. The bauxite is mined from a few metres below the ground and refined into alumina (aluminium oxide). This in turn is smelted into aluminium metal using large amounts of electricity – which is where the biggest emissions reductions can be made.